01
採寸と設計
最初の製作物はNSXのパーツ
色々と作りたいものはありますが、2Dの製図は少しできるので、まずは平面で設計して切削できる形状のものを考えたところ、NSXに使用する板状の部品が思い浮かびました。
- 今回プラグを作りたいのがこのスロットルボディ。
TRCモーターがついていたのは正方形の1点が飛び出したような形状の機械加工面で、ここに取り付ける蓋を作ります。
機能的には穴を塞ぐだけなので、ボルト穴が4つ開いた板を作ればよいのですが、機械加工面の形状にぴったり合わせたかっこいい板を作りたいわけです。
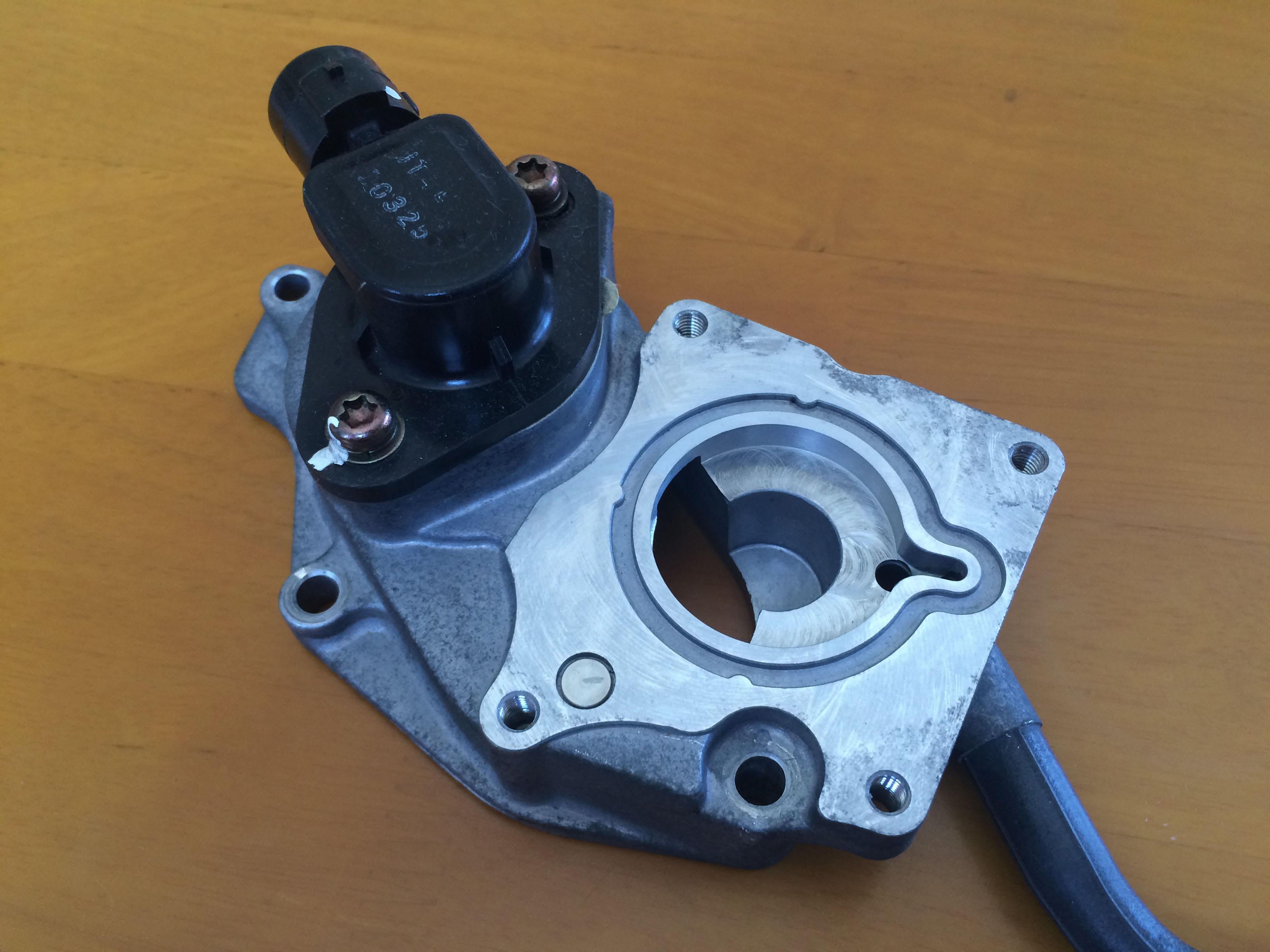
NSX用スロットルボディ
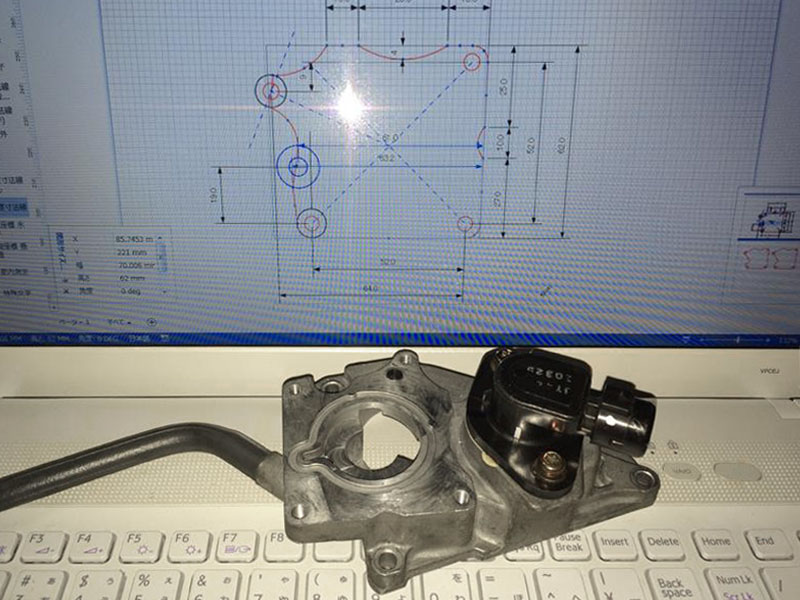
採寸しながらVisioで設計
- 変則的な形状をしていますが、物差しやノギスを使用して地道に実物を採寸しながら設計します。
2Dの場合、JWCADを使用している人が多いのですが、私が使い慣れているVisioを使用しました。
Visioは現在、Microsoft Officeの中に入っていますが、昔は単独のメーカーで1999年にMicrosoftに買収されています。 IllustratorとCADの中間のようなソフトで、お絵描きも設計もできる使いやすいソフトです。
設計が完了したら作図したデータを保存します。Visioデータ(vsd)のままでは使用できないので、DXFデータに変換します(Visio2013の場合は「AutoCAD 変換ファイル」を選択)。
02
切削データ変換
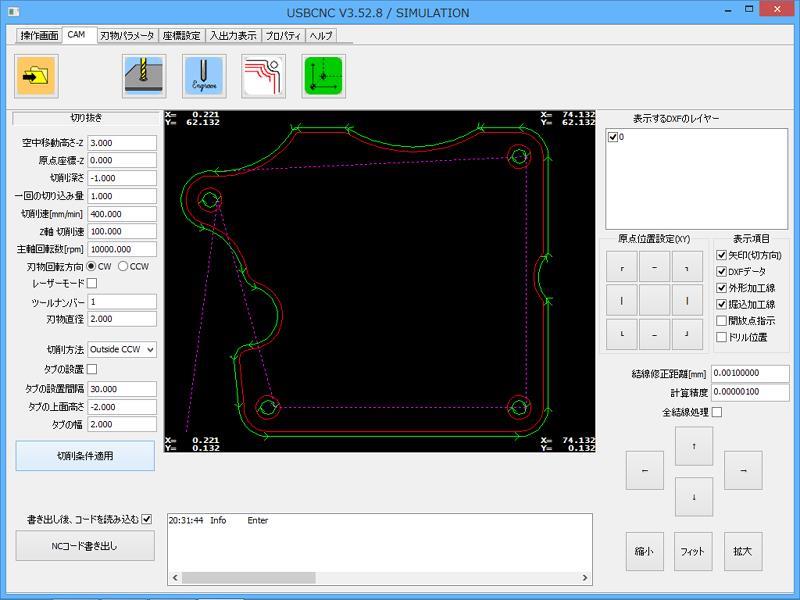
BT200付属 CAMソフト画面
- CNCで切削を行うには図面をGコードという切削指示データに変換する必要があり、変換を行うソフトをCAMソフトと呼びます。
BT200には一応2DCAMソフトが付属しています。
CAMソフトを起動してDXFファイルを読み込み、エンドミルの仕様、切削速度、切削ピッチなどの各種パラメータを設定して「切削条件適用」をクリックすると、エンドミルの軌道が自動的に設定されます。 続いて「NCコード書き出し」をクリックすると、拡張子「cnc」のGコード切削指示データが出力されます。
03
厚さ2mmのアクリル板で試作
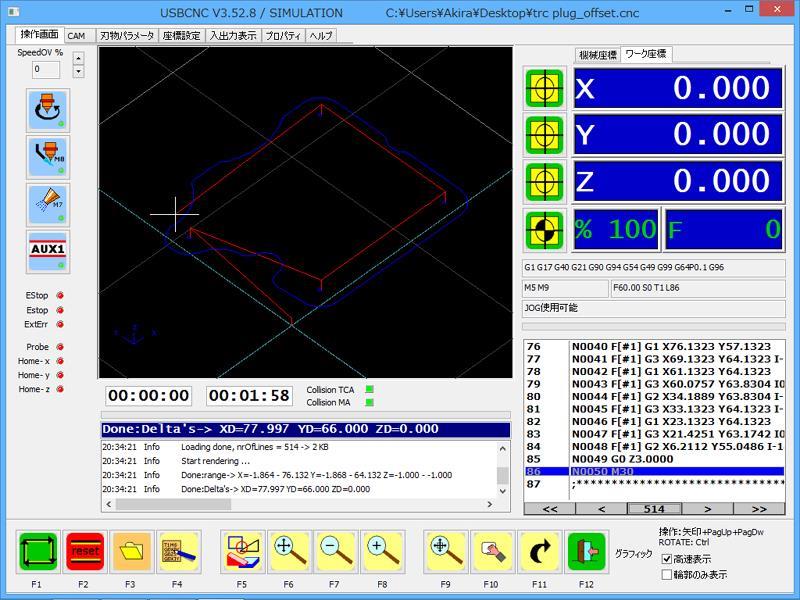
BT200付属 CAMソフト画面
- 作成した切削指示データをCNC制御ソフトで読み込むと切削スタンバイです。 画面の右下に表示されているのが切削プログラムであるGコードです。 このソフト上ではCNCの手動操作、切削スピードの調整、原点の設定などが行えます。 画面の右下に表示されているのが切削プログラムであるGコードです。
- φ1のエンドミルで厚さ2mmのアクリル板を切削。
設定は、XY軸送り速度:600mm/min、Z軸送り速度:100mm/min、Z軸切削ピッチ:0.1mm。
試しにZ軸0.2mmピッチに変更してみましたが、騒音が大きいのと、たまに溶けたアクリルがエンドミルにまとわり付くので、0.1mmピッチの方がリスクが少ないと思います。 - できあがった試作品を実際の対象物に当てがって確認すると、ボルト穴位置や大まかな形状などは合っていたものの、一か所取り付け面と微妙なずれがあったので本番切削前に設計を微修正します。
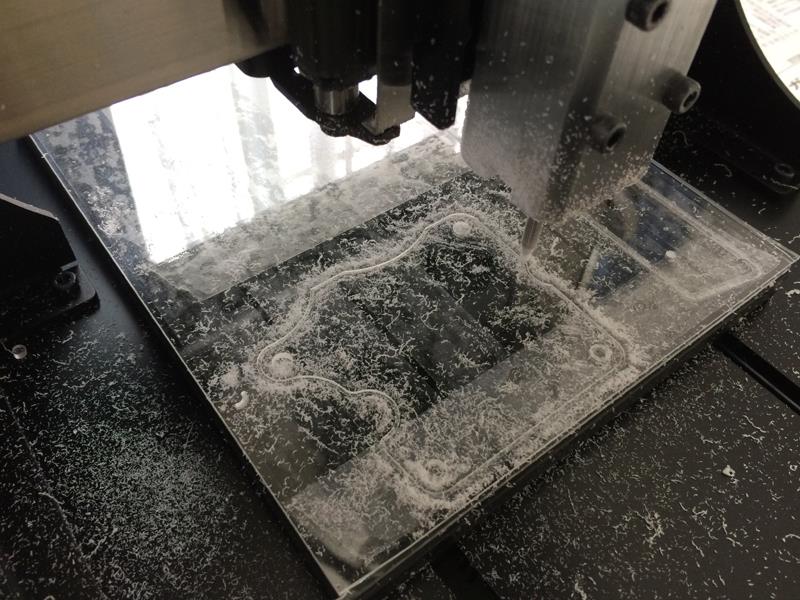
アクリル板切削
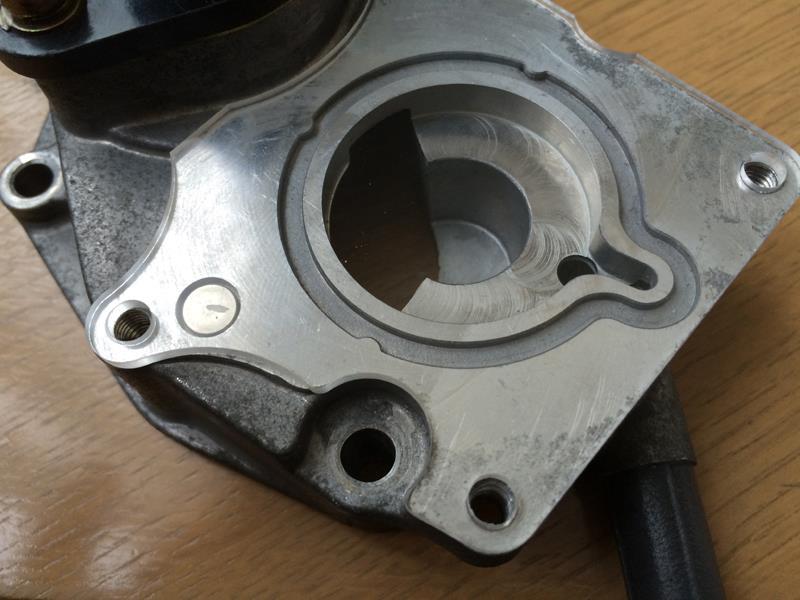
試作アクリル板の仮合わせ
04
厚さ2mmのアルミ板で試作
- アクリル試作品の形状が完成したので、アルミ製試作品の切削を行います。
まず、2mm厚のアルミ板(A5052)でドライ切削をやってみました。
とりあえずXY軸切削スピードF300、Z軸ピッチ0.1㎜に設定して切削すると切削面が汚くなりました。切削ピッチを0.05mmに落としてもあまり変わりません。
そこで切削油がわりにCRCを少し吹いてみると音も振動減って切削面がかなり綺麗になりました。上がウェット切削、下がドライ切削です。
やはり切削面の仕上がりを考えるとウェット切削は必須のようです。
ただ、仕上がりはまだまだ満足ゆくものではなく、良く見ると縦筋のような荒れがあります。
切削面改善切削面の改善をすべく、F300(XY軸)、Z軸ピッチ0.05mmの設定で試行錯誤。 水溶性の切削液を購入して使用してみましたが、目立った改善はなく、どちらかと言うとCRCの方が切削面が滑らかな気がします。 φ1のエンドミルを使用していたので、剛性に問題があるかも?と思ってφ4で切削してみても変化はなし。送り速度をF100付近まで落としてみても変化はありませんでした。
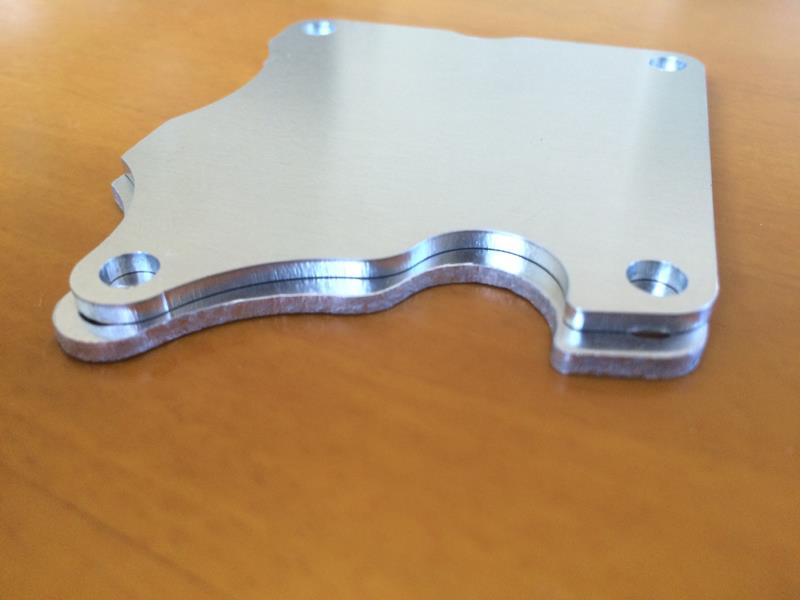
ドライ切削とウェット切削の比較
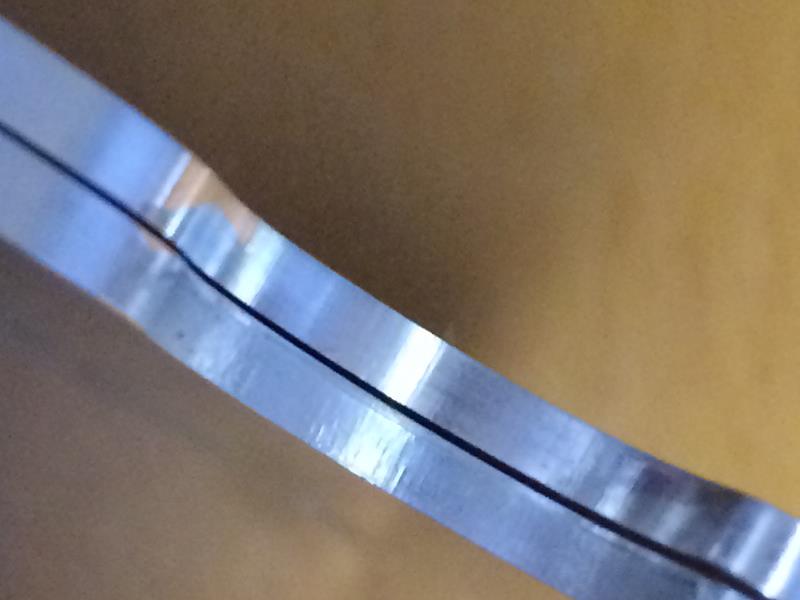
1回加工と2回加工の比較
- そこで、原点に戻ってCNC自体を組み直してみました。
最初は動きの軽さを重視してスライドシャフトを組んでいましたが、動きの重さを無視してガタゼロを目指してみました。
すると騒音がかなり軽減したのですが、切削面はほんの少しだけ綺麗になったような気がする程度の微妙な変化のみ。
粗削りと仕上げ工程を分けないとダメなのではないかと考え、仕上がり寸法の0.2㎜オーバーで一旦切削し、仕上げで0.2㎜分をXY軸切削スピードF300、Z軸ピッチ0.5mmでもう一度切削してみるとすごく綺麗に仕上がりました。写真の上が2回加工、下が1回加工。 一発加工では切削した溝にエンドミルがフィットしているから機械的なブレが影響するのか、切削面の仕上がりがかなり違います。