01
ポケットの設計と加工工程
いかにもそれらしいポケットを追加
実際使用する部品はテストで切削した板より厚い4mmのものを使用します。ただの板では面白くないので、ポケット加工をして肉抜きを行います。
材料として使用するアルミはA5052で、対腐食性に優れ、切削性が良いという性質があります。強度が必要な部品であればA2017(俗にいうジェラルミン)が適切ですが、A5052より対腐食性が劣ります。
BT-200付属のCAMソフトには「仕上げ削りしろ」という設定項目がありますが、これはZ軸の切削ピッチに関係なく材料の加工面にエンドミルを1回当てる削りしろのことなので注意が必要です。
例えばポケットの深さが5mmであれば、エンドミルの側面が高さ5mmの材料を1回で設定値分だけ削る動きになるので、かなり小さな値(目安としては0.1mm以内)に設定しないと失敗します。
また、ポケットの角が90°より鋭角の場合、使用するエンドミル半径+α以上でR部分を設計しないと、材料との接触面積が広くなり、高確率で過負荷により停止してしまいます。
例えばφ4mmのエンドミルを使用する場合、最低でもR2.1㎜以上に設計する必要があります。
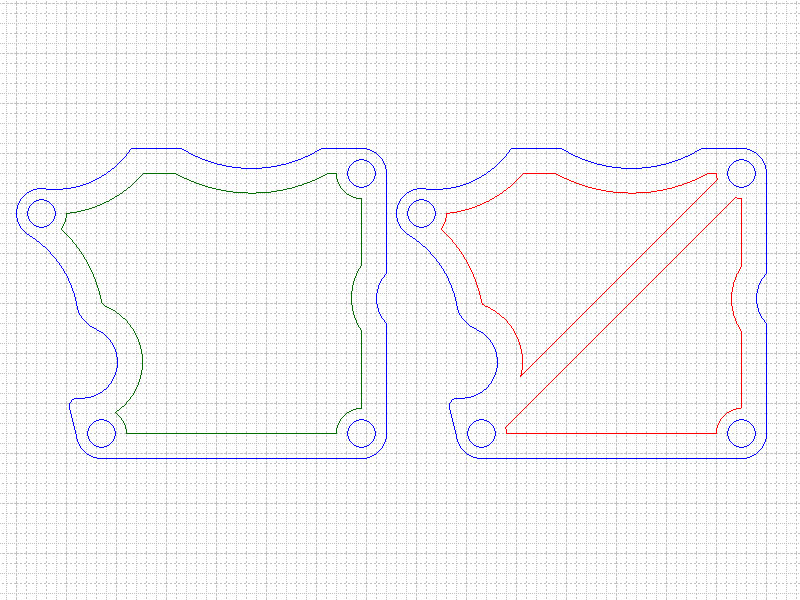
ポケット加工案
- ポケット形状の案として2案作ってみましたが、見た目のかっこよさという点だけで斜めの骨がある方(右側)を採用しました。
角の部分は鋭角になってしまっているので、エンドミル半径以上のRに修正します。
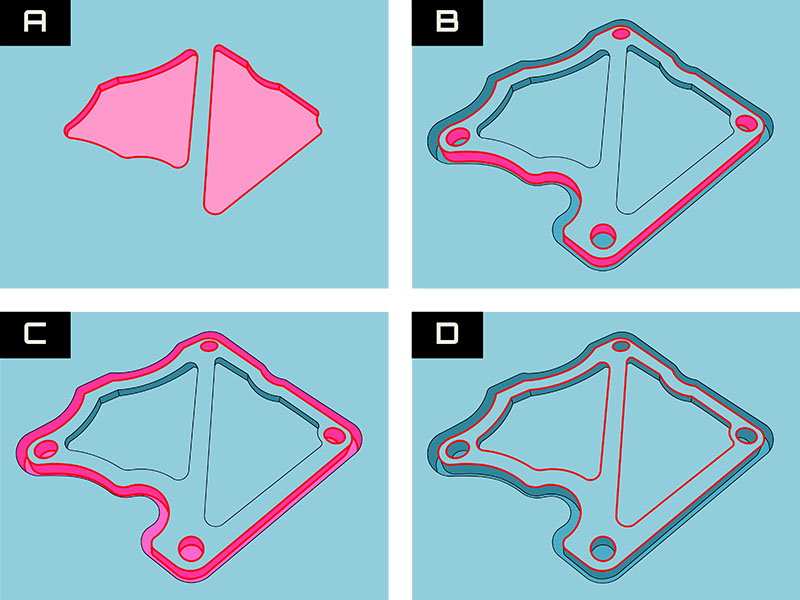
- 試作品の切削は2工程で行いましたが、ポケットの追加とエッジ部の面取りを追加するので、本番は以下の4工程で加工を行います。
A ポケット加工
B 輪郭の荒化工
C 輪郭の仕上げ加工
D エッジ部の面取り加工
今回は2DCAD(Visio)を使用しているので、工程数分の図面に分ける必要がありますが、B~Dは同じ形なので、CAMソフトのエンドミルの直径の設定値で「わざと実際の直径と異なる値にする」ことで、同一図面で行うこともできます。 今回のケースで言えば「荒加工の時に直径φ2.0mmのエンドミルを使用し、設定値はφ1.8mm」とすることで、0.1mmの仕上げ代を残した仕上がりとなります。
02
切削加工
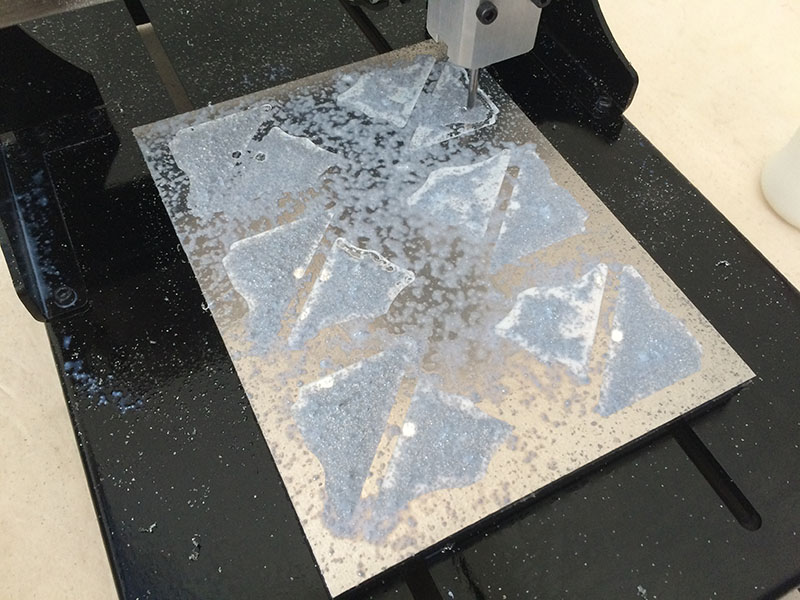
ポケットの切削加工
- 切削油を使用して加工。ポケット部分で切削油が逃げない為、多めに給油して放置できます。
ポケットだけで1枚あたりの加工時間が約1時間。一気に6個製作しているので約6時間かかります (ポケット加工は効率アップのためφ4mmを使用しています)。
水平方向の切削速度が200S(エンドミルが200mm/minで進む速度)、垂直方向の切削ピッチが0.05mmで切削しました。 - 輪郭部分を粗加工と仕上げ加工に分けて切削し、最後にエッジ部の面取り加工を行います。
ポケット加工と違って切削油が切れやすいので、所々で様子を見て給油しながらの作業になります。
この工程が約7~8時間で、6枚の合計製作時間は14時間になります。 - 加工範囲にぎりぎり6枚収まったので、同じものが欲しい人に譲るために6枚同時に製作中。
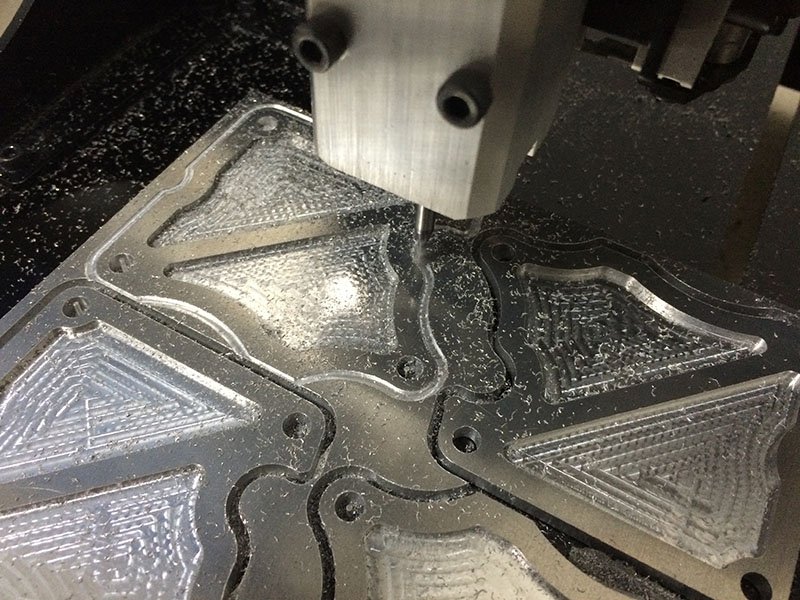
輪郭の切削加工
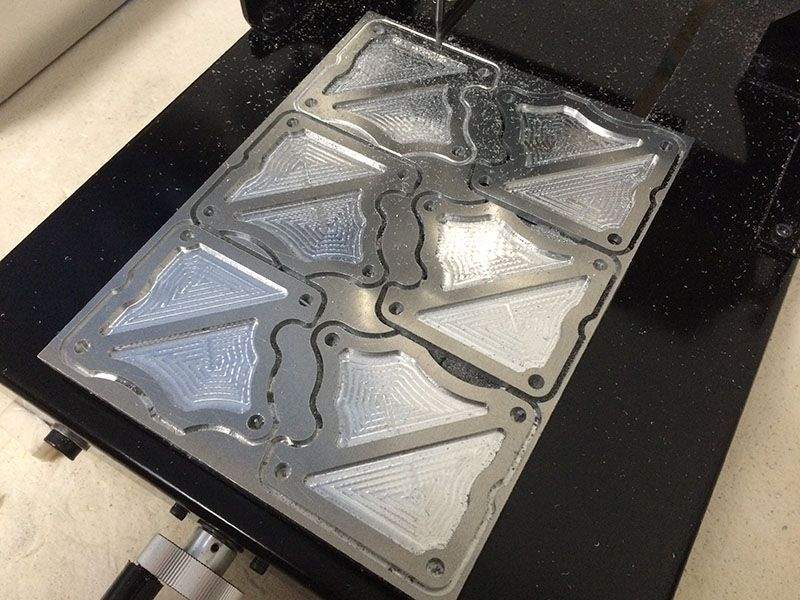
ぎりぎり加工範囲に収まる6枚を同時加工
03
完成~試着
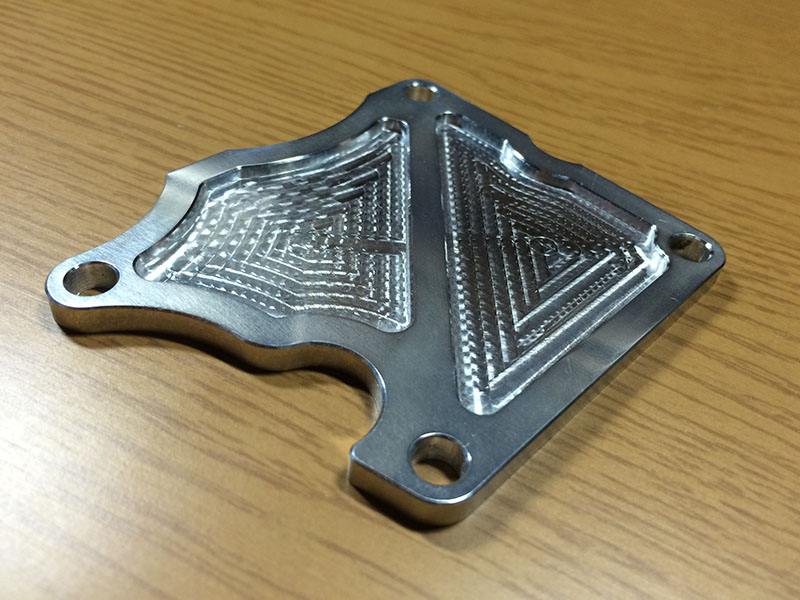
TRCモータープラグ完成品
TRCモータープラグ完成
- 長い道のりを経てやっと完成。 加工に時間は掛かりますが、1枚あたりの材料費は200円程度です。自宅でオリジナル部品の製作が実現できると思えばコストパフォーマンスは抜群です。
- 取り付け箇所に当てがってフィッティングに問題ないことを確認。目視では寸分の狂いもなく機械加工面の形状にフィットしています。
- ボルトを取り付けて、ボルト穴の芯がしっかり出ていることを確認。純正ボルトが底付きせずきちんと締まるかも確認します。
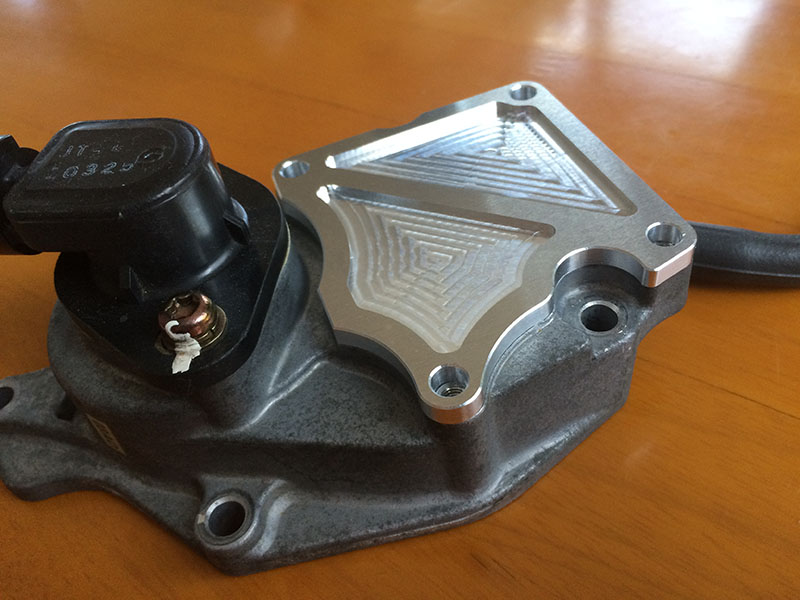
取り付け箇所に当てがって確認
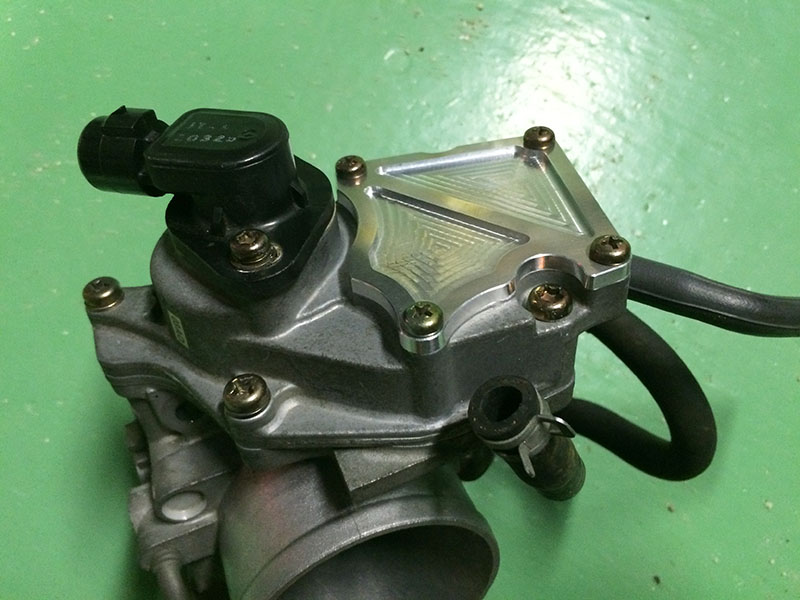
ボルトを締めて確認